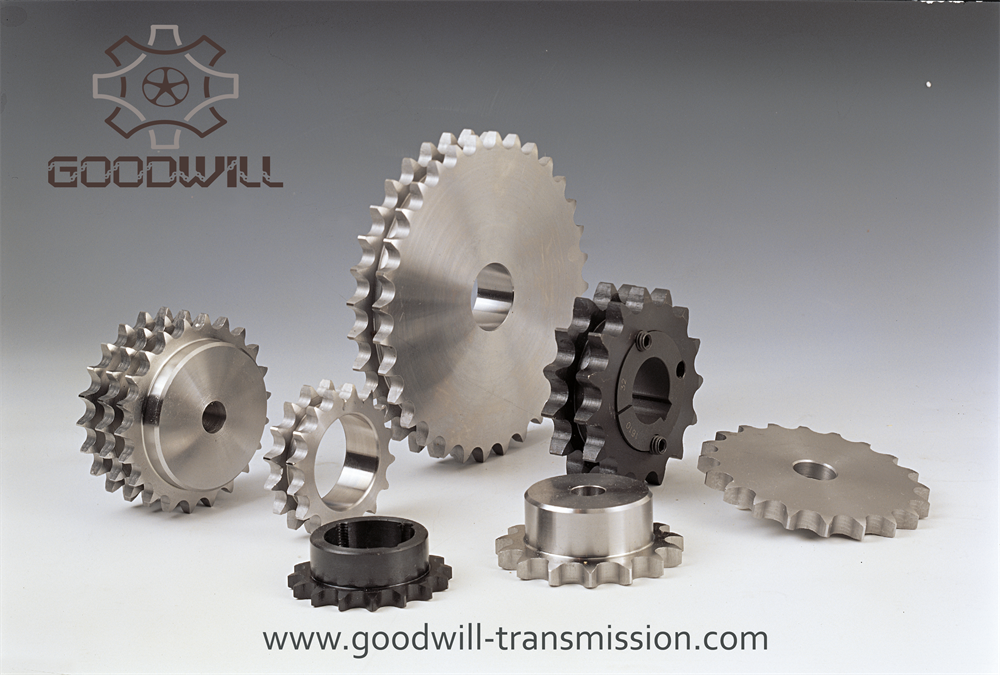
જ્યારે તમારી યાંત્રિક સિસ્ટમોની કાર્યક્ષમતા અને ટકાઉપણું વધારવાની વાત આવે છે, ત્યારે ચેઇન સ્પ્રોકેટ્સની પસંદગી સર્વોપરી છે. ચાલો સામગ્રી, પરિમાણો, માળખાં અને જાળવણીના આવશ્યક પાસાઓમાં ડૂબકી લગાવીએ જે તમારા કાર્યોને નવી ઊંચાઈઓ પર લઈ જશે.
સામગ્રીની પસંદગી: જ્યારે તમારી યાંત્રિક સિસ્ટમોને ઑપ્ટિમાઇઝ કરવાની વાત આવે છે, ત્યારે ચેઇન સ્પ્રોકેટ સામગ્રીની પસંદગી ખૂબ જ મહત્વપૂર્ણ છે. તમારે ખાતરી કરવી જોઈએ કે તમારા સ્પ્રોકેટના દાંતમાં પૂરતી સંપર્ક થાક શક્તિ અને વસ્ત્રો પ્રતિકાર હોય. એટલા માટે ઉચ્ચ-ગુણવત્તાવાળા કાર્બન સ્ટીલ, જેમ કે 45 સ્ટીલ, ઘણીવાર શ્રેષ્ઠ પસંદગી હોય છે. તે મહત્વપૂર્ણ એપ્લિકેશનો માટે, ઉન્નત પ્રદર્શન માટે 40Cr અથવા 35SiMn જેવા એલોય સ્ટીલ્સમાં અપગ્રેડ કરવાનું વિચારો.
મોટાભાગના સ્પ્રૉકેટ દાંત 40 થી 60 HRC ની સપાટીની કઠિનતા પ્રાપ્ત કરવા માટે ગરમીની સારવારમાંથી પસાર થાય છે, જે ખાતરી કરે છે કે તેઓ કામગીરીની કઠોરતાનો સામનો કરી શકે છે. એ નોંધવું મહત્વપૂર્ણ છે કે નાના સ્પ્રોકેટ તેમના મોટા સમકક્ષો કરતાં વધુ વારંવાર જોડાય છે અને વધુ અસરનો સામનો કરે છે. તેથી, નાના સ્પ્રોકેટ માટે વપરાતી સામગ્રી મોટા સ્પ્રોકેટ માટે વપરાતી સામગ્રી કરતાં શ્રેષ્ઠ હોવી જોઈએ.
એવા સ્પ્રોકેટ્સ માટે કે જેને આંચકાનો ભાર સહન કરવાની જરૂર હોય, લો-કાર્બન સ્ટીલ એક ઉત્તમ વિકલ્પ છે. બીજી બાજુ, કાસ્ટ સ્ટીલ એવા સ્પ્રોકેટ્સ માટે આદર્શ છે જે ઘસારો અનુભવે છે પરંતુ ગંભીર અસરના કંપનોનો સામનો કરતા નથી. જો તમારી એપ્લિકેશન ઉચ્ચ શક્તિ અને ઘસારો પ્રતિકારની માંગ કરે છે, તો એલોય સ્ટીલ એ શ્રેષ્ઠ વિકલ્પ છે.
તમારા ચેઇન સ્પ્રૉકેટ્સ માટે યોગ્ય સામગ્રીમાં રોકાણ કરવાથી તેમની આયુષ્ય વધે છે એટલું જ નહીં પરંતુ તમારી યાંત્રિક સિસ્ટમ્સની એકંદર કાર્યક્ષમતામાં પણ વધારો થાય છે. ગુણવત્તા સાથે સમાધાન કરશો નહીં - સમજદારીપૂર્વક પસંદ કરો અને તમારા પ્રદર્શનને ઉંચુ થતું જુઓ!
મુખ્ય પરિમાણો અને માળખાકીય પસંદગીઓ
શ્રેષ્ઠ કામગીરી માટે તમારા સ્પ્રોકેટ્સના પ્રાથમિક પરિમાણોને સમજવું જરૂરી છે. મુખ્ય પરિમાણોમાં દાંતની સંખ્યા, પિચ સર્કલ વ્યાસ, બાહ્ય વ્યાસ, મૂળ વ્યાસ, પિચ બહુકોણ ઉપર દાંતની ઊંચાઈ અને દાંતની પહોળાઈનો સમાવેશ થાય છે. પિચ સર્કલ એ વર્તુળ છે જેના પર ચેઇન પિનનું કેન્દ્ર આવેલું છે, જે ચેઇન પિચ દ્વારા સમાનરૂપે વિભાજિત થાય છે.નીચે બતાવ્યા પ્રમાણે:

સ્પ્રોકેટ્સ વિવિધ માળખાકીય સ્વરૂપોમાં આવે છે, જેમાં ઘન, છિદ્રિત, વેલ્ડેડ અને એસેમ્બલ પ્રકારોનો સમાવેશ થાય છે. કદના આધારે, તમે યોગ્ય માળખું પસંદ કરી શકો છો: નાના વ્યાસના સ્પ્રોકેટ્સ ઘન હોઈ શકે છે, મધ્યમ વ્યાસના સ્પ્રોકેટ્સ ઘણીવાર છિદ્રિત ડિઝાઇનનો ઉપયોગ કરે છે, અને મોટા વ્યાસના સ્પ્રોકેટ્સ સામાન્ય રીતે ટૂથ રિંગ અને કોર માટે વિવિધ સામગ્રીને જોડે છે, જે વેલ્ડીંગ અથવા બોલ્ટિંગ દ્વારા જોડાયેલા હોય છે. ચોક્કસ ઉદાહરણો માટે, ગુડવિલ'સ તપાસો.સ્પ્રોકેટકેટલોગ.
દાંતની ડિઝાઇન: કાર્યક્ષમતાનું હૃદય
સ્પ્રોકેટ પર દાંતની સંખ્યા ટ્રાન્સમિશન સ્મૂથનેસ અને એકંદર આયુષ્ય પર નોંધપાત્ર અસર કરે છે. યોગ્ય સંખ્યામાં દાંત પસંદ કરવા ખૂબ જ મહત્વપૂર્ણ છે - ખૂબ વધારે નહીં અને ખૂબ ઓછા નહીં. વધુ પડતા દાંત સાંકળનું આયુષ્ય ઘટાડી શકે છે, જ્યારે ખૂબ ઓછા દાંત અસમાનતા અને ગતિશીલ ભારમાં વધારો તરફ દોરી શકે છે. આ સમસ્યાઓને ઘટાડવા માટે, નાના સ્પ્રોકેટ પર દાંતની લઘુત્તમ સંખ્યા મર્યાદિત કરવાની સલાહ આપવામાં આવે છે, જે સામાન્ય રીતે Zmin ≥ 9 પર સેટ કરવામાં આવે છે. નાના સ્પ્રોકેટ (Z1) પર દાંતની સંખ્યા સાંકળની ગતિના આધારે પસંદ કરી શકાય છે, અને પછી મોટા સ્પ્રોકેટ (Z2) પર દાંતની સંખ્યા ટ્રાન્સમિશન રેશિયો (Z2 = iZ) નો ઉપયોગ કરીને નક્કી કરી શકાય છે. સમાન ઘસારો માટે, સ્પ્રોકેટ દાંત સામાન્ય રીતે એક વિચિત્ર સંખ્યા હોવા જોઈએ.

શ્રેષ્ઠ ચેઇન ડ્રાઇવ લેઆઉટ
તમારા ચેઇન ડ્રાઇવનું લેઆઉટ ઘટકો જેટલું જ મહત્વપૂર્ણ છે. ચેઇન ડ્રાઇવનું સામાન્ય લેઆઉટ નીચે બતાવેલ છે.

આડું લેઆઉટ: ખાતરી કરો કે બંને સ્પ્રૉકેટના પરિભ્રમણ વિમાનો એક જ ઊભી વિમાનમાં ગોઠવાયેલા છે અને તેમની અક્ષો સમાંતર છે જેથી સાંકળ છૂટી ન જાય અને અસામાન્ય ઘસારો ન થાય.
ઢાળવાળી લેઆઉટ: બે સ્પ્રોકેટની મધ્યરેખાઓ અને આડી રેખા વચ્ચેનો ખૂણો શક્ય તેટલો નાનો રાખો, આદર્શ રીતે 45° કરતા ઓછો, જેથી નીચલા સ્પ્રોકેટનું ખરાબ જોડાણ ટાળી શકાય.
ઊભી ગોઠવણી: બે સ્પ્રોકેટ્સની મધ્યરેખાઓ 90°ના ખૂણા પર રાખવાનું ટાળો; તેના બદલે, ઉપલા અને નીચલા સ્પ્રોકેટને એક બાજુ સહેજ સરભર કરો.
સાંકળની સ્થિતિ: સાંકળની કડક બાજુ ઉપર અને ઢીલી બાજુ નીચે રાખો જેથી વધુ પડતું ઢળતું ન રહે, જેનાથી સ્પ્રૉકેટ દાંતમાં દખલ થઈ શકે છે.
શ્રેષ્ઠ પ્રદર્શન માટે ટેન્શનિંગ
વધુ પડતા ઢળતા અટકાવવા માટે ચેઇન ડ્રાઇવનું યોગ્ય ટેન્શનિંગ ખૂબ જ મહત્વપૂર્ણ છે, જેનાથી ખરાબ જોડાણ અને કંપન થઈ શકે છે. જ્યારે બે સ્પ્રૉકેટની અક્ષો વચ્ચેનો ખૂણો 60° કરતાં વધી જાય છે, ત્યારે સામાન્ય રીતે ટેન્શનિંગ ડિવાઇસનો ઉપયોગ કરવામાં આવે છે.
ટેન્શનિંગ માટે વિવિધ પદ્ધતિઓ છે, જેમાં સૌથી સામાન્ય છે કેન્દ્ર અંતરને સમાયોજિત કરવું અને ટેન્શનિંગ ઉપકરણોનો ઉપયોગ કરવો. જો કેન્દ્ર અંતર એડજસ્ટેબલ હોય, તો તમે ઇચ્છિત ટેન્શન પ્રાપ્ત કરવા માટે તેમાં ફેરફાર કરી શકો છો. જો નહીં, તો ટેન્શનને સમાયોજિત કરવા માટે ટેન્શનિંગ વ્હીલ ઉમેરી શકાય છે. આ વ્હીલ નાના સ્પ્રૉકેટની સ્લેક બાજુની નજીક મૂકવું જોઈએ, અને તેનો વ્યાસ નાના સ્પ્રૉકેટ જેવો હોવો જોઈએ.
લુબ્રિકેશનનું મહત્વ
ચેઇન ડ્રાઇવના શ્રેષ્ઠ પ્રદર્શન માટે લુબ્રિકેશન આવશ્યક છે, ખાસ કરીને હાઇ-સ્પીડ અને હેવી-લોડ એપ્લિકેશન્સમાં. યોગ્ય લુબ્રિકેશન ઘસારો નોંધપાત્ર રીતે ઘટાડે છે, અસર ઘટાડે છે, લોડ ક્ષમતા વધારે છે અને ચેઇનનું આયુષ્ય લંબાવે છે. તેથી, કાર્યક્ષમ કામગીરી સુનિશ્ચિત કરવા માટે યોગ્ય લુબ્રિકેશન પદ્ધતિ અને લુબ્રિકન્ટનો પ્રકાર પસંદ કરવો મહત્વપૂર્ણ છે.
લુબ્રિકેશન પદ્ધતિઓ:
નિયમિત મેન્યુઅલ લુબ્રિકેશન: આ પદ્ધતિમાં ઓઇલ કેન અથવા બ્રશનો ઉપયોગ કરીને સાંકળની સ્લેક બાજુ પર આંતરિક અને બાહ્ય લિંક પ્લેટો વચ્ચેના ગાબડા પર તેલ લગાવવાનો સમાવેશ થાય છે. આ કાર્ય દરેક શિફ્ટમાં એકવાર કરવાની ભલામણ કરવામાં આવે છે. આ પદ્ધતિ v ≤ 4 m/s ની સાંકળ ગતિવાળા બિન-ક્રિટિકલ ડ્રાઇવ્સ માટે યોગ્ય છે.
ડ્રિપ ઓઇલ ફીડ લુબ્રિકેશન: આ સિસ્ટમમાં એક સરળ બાહ્ય કેસીંગ છે, જ્યાં તેલ કપ અને પાઇપ દ્વારા સ્લેક બાજુ પર આંતરિક અને બાહ્ય લિંક પ્લેટો વચ્ચેના ગાબડામાં તેલ નાખવામાં આવે છે. સિંગલ-રો ચેઇન માટે, તેલ પુરવઠો દર સામાન્ય રીતે પ્રતિ મિનિટ 5-20 ટીપાં હોય છે, જેમાં મહત્તમ મૂલ્ય વધુ ઝડપે વપરાય છે. આ પદ્ધતિ v ≤ 10 m/s ની ચેઇન ગતિવાળા ડ્રાઇવ માટે યોગ્ય છે.
ઓઇલ બાથ લુબ્રિકેશન: આ પદ્ધતિમાં, લીક ન થતું બાહ્ય આવરણ સાંકળને સીલબંધ તેલ ભંડારમાંથી પસાર થવા દે છે. સાંકળને ખૂબ ઊંડાણમાં ડૂબાડવાનું ટાળવા માટે કાળજી લેવી જોઈએ, કારણ કે વધુ પડતા નિમજ્જનથી હલનચલનને કારણે તેલનું નોંધપાત્ર નુકસાન થઈ શકે છે અને તેલ વધુ ગરમ થઈ શકે છે અને બગડી શકે છે. સામાન્ય રીતે 6-12 મીમીની નિમજ્જન ઊંડાઈની ભલામણ કરવામાં આવે છે, જે આ પદ્ધતિને v = 6-12 m/s ની સાંકળ ગતિવાળા ડ્રાઇવ માટે યોગ્ય બનાવે છે.
સ્પ્લેશ ઓઇલ ફીડ લુબ્રિકેશન: આ તકનીકમાં સીલબંધ કન્ટેનરનો ઉપયોગ થાય છે જ્યાં સ્પ્લેશ પ્લેટ દ્વારા તેલ છાંટાવામાં આવે છે. ત્યારબાદ તેલને કેસીંગ પરના તેલ સંગ્રહ ઉપકરણ દ્વારા સાંકળ તરફ નિર્દેશિત કરવામાં આવે છે. સ્પ્લેશ પ્લેટની નિમજ્જન ઊંડાઈ 12-15 મીમી જાળવી રાખવી જોઈએ, અને અસરકારક લુબ્રિકેશન સુનિશ્ચિત કરવા માટે સ્પ્લેશ પ્લેટની ગતિ 3 મીટર/સેકન્ડથી વધુ હોવી જોઈએ.
પ્રેશર લુબ્રિકેશન: આ અદ્યતન પદ્ધતિમાં, તેલ પંપનો ઉપયોગ કરીને સાંકળ પર તેલ છાંટવામાં આવે છે, જેમાં નોઝલ વ્યૂહાત્મક રીતે તે બિંદુ પર સ્થિત હોય છે જ્યાં સાંકળ જોડાય છે. ફરતું તેલ માત્ર લુબ્રિકેટ જ નહીં પણ ઠંડક અસર પણ પ્રદાન કરે છે. દરેક નોઝલ માટે તેલ પુરવઠો સંબંધિત માર્ગદર્શિકાઓનો ઉપયોગ કરીને સાંકળની પિચ અને ગતિના આધારે નક્કી કરી શકાય છે, જે આ પદ્ધતિને v ≥ 8 m/s ની સાંકળ ગતિ સાથે ઉચ્ચ-શક્તિવાળા ડ્રાઇવ માટે યોગ્ય બનાવે છે.
તમારી યાંત્રિક પ્રણાલીઓમાં શ્રેષ્ઠ કામગીરી અને કાર્યક્ષમતા પ્રાપ્ત કરવા માટે, ચેઇન સ્પ્રોકેટ પસંદગી અને જાળવણીના મહત્વપૂર્ણ પાસાઓને સમજવું જરૂરી છે. તમારા મશીનરીની સફળતાને તક પર ન છોડો - જાણકાર નિર્ણયો લો જે કાયમી પરિણામો આપે!
તમારા કામકાજ સરળતાથી અને કાર્યક્ષમ રીતે ચાલે તે સુનિશ્ચિત કરવા માટે યોગ્ય સામગ્રી, પરિમાણો અને જાળવણી વ્યૂહરચનાઓની પસંદગી કરવી એ ચાવીરૂપ છે. આ પરિબળોને પ્રાથમિકતા આપીને, તમે તમારા સાધનોની આયુષ્ય અને વિશ્વસનીયતા વધારી શકો છો.
જો તમને સ્પ્રોકેટ્સ વિશે કોઈ પ્રશ્નો હોય અથવા નિષ્ણાત માર્ગદર્શનની જરૂર હોય, તો કૃપા કરીને અમારો સંપર્ક કરવામાં અચકાશો નહીંexport@cd-goodwill.com. અમારી સમર્પિત ટીમ તમારી બધી સ્પ્રૉકેટ જરૂરિયાતોમાં મદદ કરવા માટે અહીં છે!
પોસ્ટ સમય: નવેમ્બર-21-2024